

Constant Radius Unfolding:Ĭonstant radius unfolding uses an unfolding algorithm that forces the radius and the bend centre points to be constant. Looking at the 45 degree bend from our example this is what you should expect to see. This means that when a bend is folded, the radius and the centre point must change to maintain the total length. The following example will explain the differences between the various choices using our example part.Ĭonstant length unfolding uses an unfolding algorithm that forces the length of the radius to always be constant. When each one is selected the result will be updated dynamically on the screen. When performing the step by step unfolding it is possible to choose how the bend is developed, there are actually three types that can be selected with the icon shown below. Note :- The previous operation can also be performed by right clicking the bend in the graphics area. Here you can change the Unfolding Bend Type select the right button Here you can change the neutral fibre value from the drop down list or even input the value using Input Neutral Fibre. Material is set to the current solid model and can be modified Part Thickness is set to the current solid model thickness and this cannot be modified. Part Name is set to the current solid model and can be modified The properties panel displays the current neutral fibre value for the bend. Left Click a node from the tree to reveal the properties panel. Note: - In our example we will not be modifying any of the values that appear. It is often necessary to use a different neutral fibre when there is a big difference between the bend radii on the part. Selecting a bend using the LHM button it is possible to change the neutral fibre for a single bend using the bend property window. Neutral fibre either as a constant value or using one of two automatic neutral fibre algorithms:Īlgorithm is to be used for the step-by-step unfolding.ĭisplaying and changing Neutral Fibre values for BendsĪt this stage the tree will again show all the bending stages, but also the neutral fibre at each bend. Selecting a surface the system asks to set the Material Side, but after that the procedure is exactly the same:īox will be displayed. The selection of the origin point is very important because this point will be used as reference point to following operations.Īfter the point selection the system shows the mask where set some parameters as Material, Thickness and Neutral Fibre: Keeping the default settings, the system extracts the selected skin, asking to select the face linked with origin point and then the Reference Point:
Manual pdf vero visi skin#
Here is possible set different options to obtain the skin of the Part, as create a Copy, Delete or not the original part, Search or not the Sharp Edges and then the distance between the two parts. Selecting a face from a Solid, the system loads the Extract Skin function, showing this mask: Select the origin point: Select the TOP centre point of the circle Select the Face linked with the Origin part: Select Face 1 (Top Face)

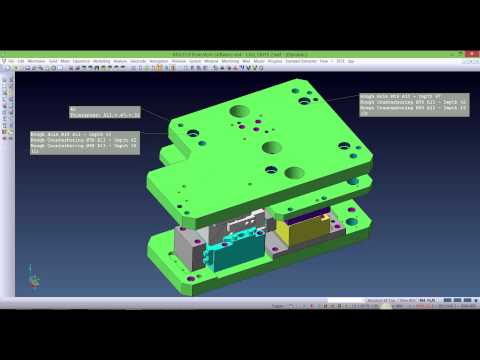
Select the part to analyse: Select part 1 (on Top Face). Please take some time to study the following interface and icon descriptions for each phase of the part management.įrom the Progress Part Manager, ensure the ‘Part Analysis’ icon is activated and select the Part Analysis Build icon Selecting the ‘Part Study’ menu will now display the new Progress interface. This document has been provided to describe in detail the new unfolding routines and interfaces for VISI-Progress that have been introduced from version 11.2 onwards.
